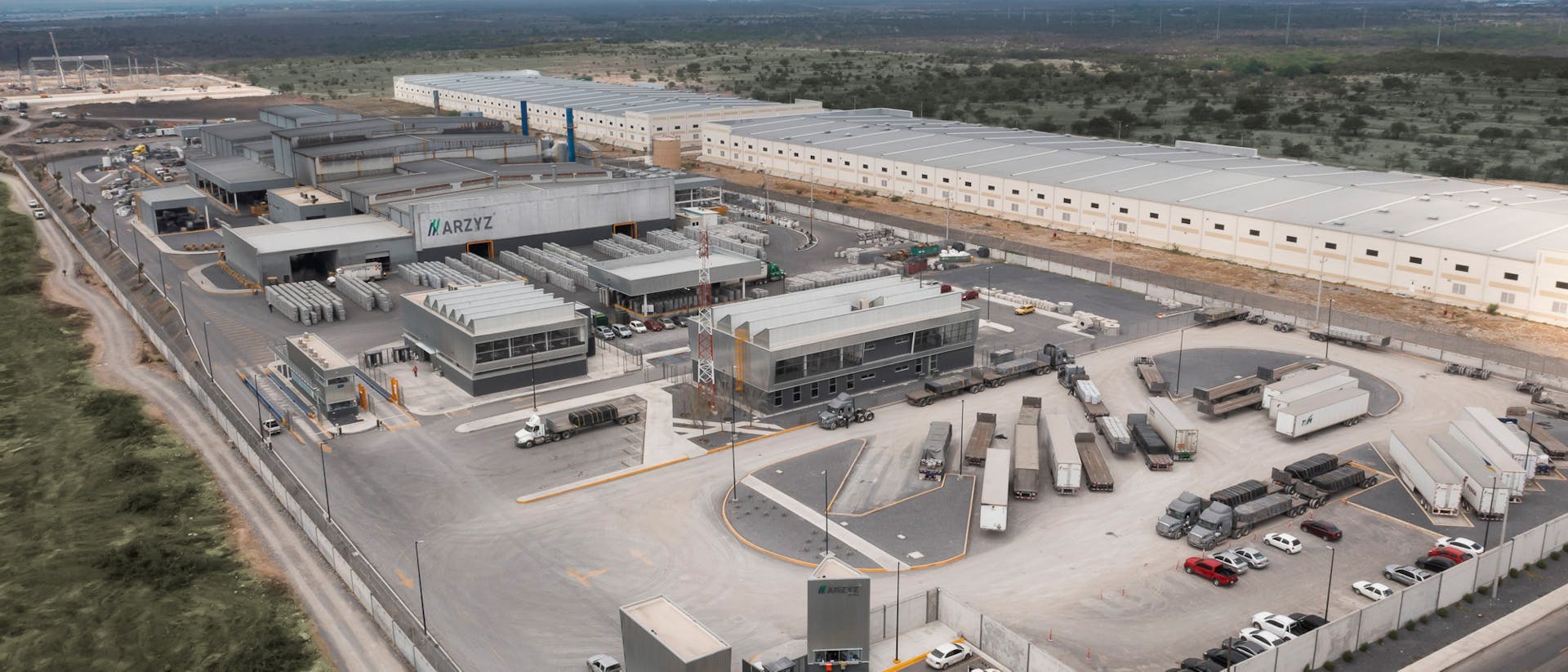
STI Engineering for ARZYZ Aluminium: Innovation and sustainability with the ARCO Project
We are proud to share our work alongside ARZYZ Aluminium in the ARCO Project, which represents a significant strategic turning point for the expansion of the North American market and the consolidation of ARZYZ as a leader in the aluminum industry.
Founded in 1980 in Mexico as a family business initially specializing in zinc trading, ARZYZ - Leading Mexico's Aluminum Industry - has grown to become a reference point in aluminum production. Today, it operates three active plants producing semi-finished products such as ingots, SOW, and cones. ARZYZ's offering also includes liquid aluminum and aluminum powders, catering to the needs of various industrial sectors.
ARZYZ’s plans include the development of an ambitious new project: the creation of a true aluminum city, with ARCO Phase I being the first step in this ambitious journey.
The objective of this first phase is to produce semi-finished products from a range of cold-rolled aluminum alloy flat products, thus expanding the product offering and opening doors to strategic markets such as Automotive, Construction, HVAC, Appliance & General Industry. This is all driven by a vision that combines innovation and sustainability.
In this initial phase of the project STI Engineering is responsible for Process Engineering, focusing on the plant layout design, optimization of production flows, and managing critical issues, thus ensuring proper material handling and equipment installation.
The ARCO Phase I project is divided into different zones, with the heart of production being the cold area, where the coil is rolled to reach the desired thickness. The central element of this area is the Cold Rolling Mill (CRM), which receives hot coils from 12 twin-roll casters from a state-of-the-art foundry featuring three distinct casting lines, organized in a melting furnace (single-chamber melting furnace) and a holding furnace (buffer for liquid metal feeding the casting machines), allowing for the simultaneous production of three different alloys across four twin roll casters.
Once cast and cold-rolled, the coil undergoes, depending on the alloy, one or more annealing processes in dedicated furnaces to homogenize the material's structure. This is followed by a surface cleaning process and flatness control via a tension leveling & cleaning machine, which unwinds the coil, eliminates residual stresses, and ensures optimal flatness. The final step is the dimensional reduction of the coil, achieved through the slitting line.
STI Engineering's contribution materialized in the graphic representation and mapping of logistics flows, which allowed for the correct identification of the various production areas. This concept forms the foundation for the future engineering development of ARCO, a project that, with solid structural, architectural, mechanical, and electrical foundations, will continue to progress through its next phases.
With the ARCO Project, ARZYZ Aluminium is preparing to play an even more impactful role in international markets, advancing a vision where innovation and sustainability intertwine to ensure a more efficient and responsible future.
Contact us for more information